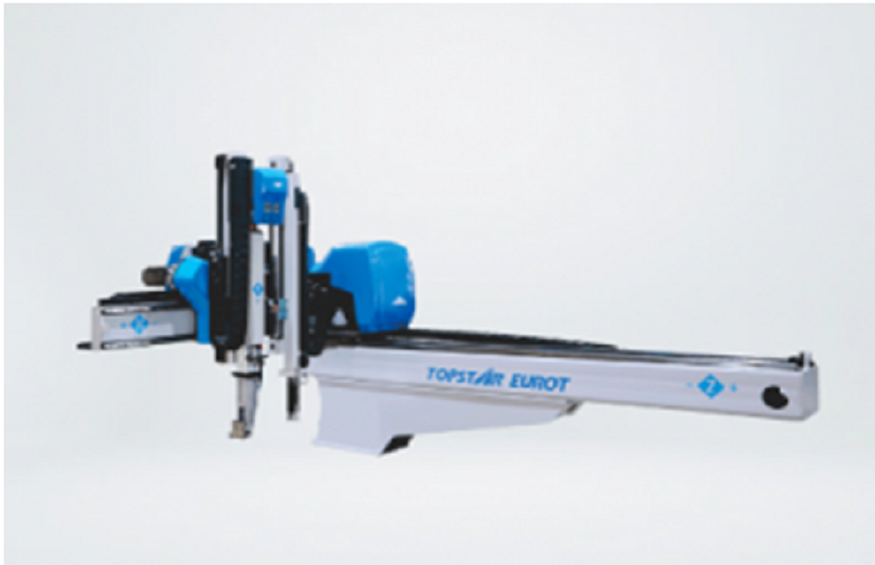
Several common robot arm injection safety tips
When operating a robot arm injection machine, it’s essential to follow safety tips. Safety is always the number one concern when it comes to using a robotic injection machine or any machinery, for that matter. The following are five common safety tips for robot arm injection machines:
Robot arms are designed to run cycles and perform tasks without human intervention
Robot arms are designed to run cycles and perform tasks without human intervention. To do so, they must be able to identify hazards in their environment and sense when an object has entered their workspace. For example, this can include sensing that a human is near or reaching into the robot arm’s workspace or detecting an object on top of a table that could fall if bumped by the robot arm.
The robot’s vision system can help with these tasks by identifying potential environmental hazards. In addition to recognizing objects such as people and other machines around them (like forklifts), robots also have sensors that allow them to detect heat sources, such as hot surfaces like ovens or pipes, so they don’t accidentally bang into them while moving around freely within their designated areas.
Robots can dispense a variety of materials.
While robots are commonly used in the automotive and medical industries, they can also be used for other purposes. Robots can dispense materials, including two-part adhesives, silicones, epoxies, and urethane potting compounds. This can include:
Two-part adhesives (e.g., epoxy)
Silicone rubber
Epoxy resin
Why are robot arms used instead of manual methods?
There are several reasons why a company might choose to use a robotic arm over other manufacturing processes. Here are just some of them:
Robots can perform tasks faster and more accurately than humans. They can repeat functions without error, which means they can go through the same process repeatedly (like thousands of times) without making mistakes. That makes robotic arms ideal for performing repetitive tasks in high-volume production environments where quality control is vital to business success.
Robots can perform tasks that humans cannot do or would be too dangerous for people to do alone. For instance, working with heavy machinery or hazardous chemicals in an industrial setting. It’s safer and easier to send a robot instead of risking injury or death by sending your employees into harm’s way every day—and then having to pay medical bills if something goes wrong!
What is a safety tip for robot arms?
A safety tip is a simple and effective way to ensure safety.
Safety tips can be as simple as a guard, like a hood that covers the end of your robot arm while not in use. Some are more complex and involve multiple components working together to minimize risk. These can include an auto-start system or a fire suppression system. The most important thing about safety tips is that they’re easy to use, understand, implement, and maintain.
1. st Safety Tip – Safety Guards
Safety guards are used to preventing injury. They must be installed to meet safety regulations and inspected regularly. If a safety guard is damaged, it should be replaced. Safety guards should not be tampered with or removed for any reason unless the robot arm is serviced by a trained professional.
2. nd Safety Tip – Expansion Rooms
An expansion room is an area of the robot arm that a human operator can access to fix any issues with the robot arm. The expansion room needs to be big enough so that humans can move freely but not so big that it will increase the system’s overall weight. To calculate the size of your expansion room, you must use essential physics and trigonometry. It is best to consider how much space is required for wiring and other components in this area. And whether there is enough storage space for tools or parts needed to maintain the robot arm.
Suppose you’re building a new facility with an existing line already installed. This case is based on previous experience in using similar systems in production environments. You may have enough knowledge of what kind of space is most suitable for work. If not – don’t worry too much! Most modern facilities come equipped with engineers who specialize in designing effective safety measures like these. Hence, they’re usually pretty good at determining how best to meet their client’s needs while keeping costs down. The key is ensuring everyone knows where each person should go when something goes wrong. Whether it’s someone accidentally cutting through live wires or getting stuck under metal beams falling apart due to lack of maintenance over time.”
3. rd Safety Tip – Fire Suppression Systems
Fire suppression systems are designed to stop a fire in its tracks. You must have one if you’re working in an environment with a fire risk. A fire suppression system works by containing the flames with a blanket of inert gas (no oxygen), which smothers and extinguishes them before they can spread.
It’s not just about stopping a fire—fire suppression systems can also help to avoid injuries caused by fumes released during a blaze. Without proper ventilation, those fumes can become toxic and cause harm to humans or animals nearby.
The benefits of having a fire suppression system installed at your facility include the following:
There are some common safety tips for robot arm injection machines
Safety guards are a must when it comes to robot arm injection machines. You should always ensure that the device has a safety guard on the head of the robot arm. This will keep you safe from any potential injury.
Ensure your company installs an expansion room for each robot arm injection machine. An expansion room is also known as an explosion enclosure and can protect workers from possible explosions or other accidents that could occur during the operation of these machines.
Fire suppression systems are also recommended when there is a fire risk at work sites where these machines are located or used regularly.
The main thrust of this article
The takeaway from this article is that robot arms are very versatile machines and can be used for many different applications. However, following proper safety precautions when using these machines is essential.